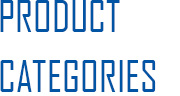
- DHP419 Series of PP Yarn Stretching Machine
- DH419D Series PP FDY Multifilament Spinning Machine HT
- DHP418 Series PP FDY Multifilament Spinning Machine MT
- DHKV 1235-12 Polyester POY Spinning Line
- DHPE Ultra High Molecular Weight Polyethylene Yarn Spinning Equipment
- DHTA Aramid 1414 Yarn Spinning Line
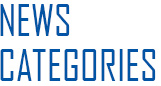
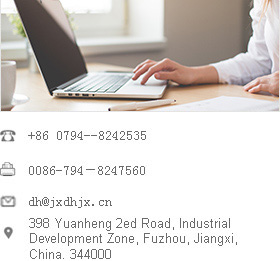
Polypropylene spinning machine process
First, the drying process
1, polypropylene spinning machine process requirements: mainly:
1. Sliced water after drying: <35PPM
2. The characteristic viscosity drop after drying: <0.02 Equipment: ROSIN drying equipment Imitation BM drying equipment
Process conditions:
(1) Pre-crystallization temperature: between the glass transition temperature and melting point of the slice, generally controlled at 160-180 degrees. (2) Pre-crystallization time: 8-30min, adjusted according to needs. (3) Pre-crystallization boiling bed wind pressure :-5-0(cmwg)
(4) Drying temperature: the higher the temperature, the better the drying effect. However, too high will affect the viscosity drop and color of the slice, generally controlled at 160-185 degrees.
(5) Drying time: make the cut water content close to equilibrium water, generally controlled at 4-12(H). (6) Dry air dew point: the lower the dew point, the better the drying effect. Generally controlled at <-30 degrees. (7 Dry air pressure: generally controlled at 0.6~3.3kgf/cm2 I. Spinning process
1. Process requirements: Mainly: oil-free characteristic viscosity drop <0.04.
2, equipment: Japan Teijin. Japan Toray. Japan Murata. Germany Barmag and domestic equipment. 3, process conditions:
(1) Screw extrusion temperature in each zone
A: Feeding section temperature: slice melting point temperature + (0-20) degrees B: compression, metering section temperature: + (10-40) degrees.
(2) Measuring head pressure of screw extruder: It is necessary to ensure the constant discharge volume of the metering pump and reduce the energy consumption. Generally, it is controlled at: 8-12mpa spinning box temperature: heating with biphenyl steam to keep the melt temperature not lowered , generally controlled at: 285-298 degrees. (3) component pressure: one control at: 12~28mpa (4) pump supply and speed
Pump supply (g/min) = spinning speed (m/min) * finished product fineness (dtex) * N divided by 1000
Metering pump speed (RPM) = pump supply (g / mig) divided by melt density (G / CM3) * pump specifications (CM3 / R) * pump efficiency (%) (5) cooling hair dryer
A: Wind speed: too large or too low will increase the fiber slack unevenness rate, generally controlled at 0.3-0.7M/S.
B: Wind temperature: keep the melt cooling flow length is not too long, try to reduce the deviation of the cooling length between the individual filaments, generally controlled at 20-28 degrees.
C: rheumatism (relative humidity), generally controlled at 60-90 (%) D: wind pressure: generally controlled at 450~600PA
(6) Stretching process: determined by a combination of factors such as the quality of the product (such as physical indicators and appearance dyeing) and production costs.